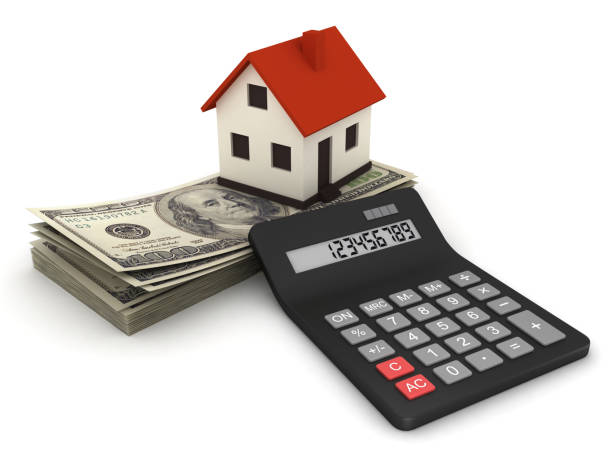
How To Estimate Equipment Cost In Construction
Estimating equipment costs accurately is crucial for the success of any construction project. Whether you’re a project manager, a contractor, or an entrepreneur venturing into the construction industry, understanding how to estimate equipment costs can significantly affect your project’s budget and timeline. This blog post will guide you through the process of equipment cost estimation, providing valuable insights, practical tips, and relevant examples tailored specifically for people in the construction industry.
Why Accurate Equipment Cost Estimation Matters
Accurate equipment cost estimation is vital for several reasons. Firstly, it ensures that you allocate sufficient budget for your project, avoiding unexpected expenses that could increase costs. Secondly, it helps in planning and scheduling, ensuring that the right equipment is available when needed. Lastly, it aids in bidding and contract negotiation, allowing you to make competitive bids while ensuring profitability.
Understanding Equipment Costs
Before you can estimate equipment costs, it’s important to understand what these costs entail. Equipment costs can be broadly categorized into two types: ownership costs and operating costs. Ownership costs include the purchase price, financing costs, insurance, taxes, and depreciation. Operating costs encompass fuel, maintenance, repairs, and operator wages.
Ownership Costs
Ownership costs are the expenses associated with owning the equipment. These costs are typically fixed and remain constant regardless of how much the equipment is used. Calculating ownership costs involves several factors:
- Purchase Price: The initial cost of buying the equipment.
- Financing Costs: Interest payments if the equipment is financed through a loan.
- Insurance: The cost of insuring the equipment against theft, damage, and liability.
- Taxes: Property taxes or other taxes imposed on the equipment.
- Depreciation: The reduction in the equipment’s value over time due to wear and tear.
Operating Costs
Operating costs are variable expenses that depend on the amount of use the equipment receives. These costs include:
- Fuel: The cost of fuel to operate the equipment.
- Maintenance: Routine maintenance costs to keep the equipment in good working condition.
- Repairs: Costs associated with fixing any breakdowns or malfunctions.
- Operator Wages: The cost of paying the operator who runs the equipment.
Steps to Estimate Equipment Costs
Estimating equipment costs involves several steps, each of which requires careful consideration and analysis. Here’s a step-by-step guide:
Step 1: Determine Equipment Needs
The first step in estimating equipment costs is determining what equipment is needed for your project. This involves analyzing the project requirements, scope, and timeline to identify the types and quantity of equipment required.
Step 2: Research Equipment Prices
Once you have identified the necessary equipment, research the market prices for purchasing or renting the equipment. Obtain quotes from multiple suppliers to get a sense of the price range and consider any additional costs such as delivery and setup fees.
Step 3: Calculate Ownership Costs
If you plan to purchase the equipment, calculate the ownership costs. This includes the purchase price, financing costs, insurance, taxes, and depreciation. Use standard formulas or online calculators to determine these costs accurately.
Step 4: Estimate Operating Costs
Next, estimate the operating costs based on the expected usage of the equipment. Consider factors such as fuel consumption, maintenance schedules, repair costs, and operator wages. Use historical data or industry benchmarks to make informed estimates.
Step 5: Factor in Contingencies
It’s important to include a contingency allowance in your equipment cost estimate to cover any unexpected expenses or price fluctuations. A common practice is to add a percentage (e.g., 10%) to the total estimated cost as a contingency.
Step 6: Review and Adjust
Finally, review your equipment cost estimates and adjust them as necessary. Consider factors such as changes in project scope, market conditions, and any feedback from stakeholders. Make sure your estimates are realistic and align with your project budget.
Common Pitfalls in Equipment Cost Estimation
While estimating equipment costs is essential, there are common pitfalls that you should be aware of to avoid costly mistakes. Here are some of the most common pitfalls:
Underestimating Maintenance and Repair Costs
One common pitfall is underestimating the costs associated with maintaining and repairing equipment. Regular maintenance is crucial to keeping equipment in good working condition and preventing breakdowns. However, it’s easy to overlook these costs or assume they will be minimal. Be sure to include accurate estimates for maintenance and repair costs in your overall equipment cost calculation.
Ignoring Depreciation
Depreciation is another factor that is often overlooked in equipment cost estimation. Over time, equipment loses value due to wear and tear. Ignoring depreciation can lead to an inaccurate estimate of ownership costs and impact the financial viability of your project. Use standard depreciation methods to account for the reduction in equipment value over time.
Failing to Include Contingencies
Contingencies are an important aspect of cost estimation that many people neglect. Unexpected expenses can arise during a project, such as equipment breakdowns, price fluctuations, or delays. Failing to include a contingency allowance in your estimate can result in budget overruns and financial strain. Always add a contingency percentage to your total estimated cost to cover unforeseen expenses.
Best Practices for Accurate Equipment Cost Estimation
To ensure accurate equipment cost estimation, follow these best practices:
Use Historical Data
Historical data from previous projects can be a valuable resource for estimating equipment costs. Analyze past projects to identify trends, cost patterns, and any factors that may have influenced equipment costs. This data can provide a benchmark for your current project and help you make more accurate estimates.
Leverage Technology
Technology can play a significant role in improving the accuracy of equipment cost estimation. Use specialized software and tools designed for construction cost estimation to streamline the process. These tools can provide detailed cost breakdowns, automate calculations, and generate reports that help in decision-making.
Collaborate with Experts
Collaborating with experts and stakeholders can enhance the accuracy of your equipment cost estimates. Consult with equipment suppliers, operators, and maintenance personnel to gather insights and verify your estimates. Their expertise can provide valuable input and help you identify any potential cost factors you may have overlooked.
Real-World Examples of Equipment Cost Estimation
To illustrate the process of equipment cost estimation, let’s look at a couple of real-world examples:
Example 1: Estimating Costs for a Bulldozer
Suppose you need a bulldozer for a construction project. Here’s how you would estimate the costs:
- Determine Equipment Needs: Identify the specific type and model of bulldozer required for the project.
- Research Equipment Prices: Obtain quotes from multiple suppliers for purchasing or renting the bulldozer.
- Calculate Ownership Costs:
- Purchase Price: $250,000
- Financing Costs: $5,000 per year
- Insurance: $3,000 per year
- Taxes: $2,000 per year
- Depreciation: $20,000 per year
- Estimate Operating Costs:
- Fuel: $500 per week
- Maintenance: $1,000 per month
- Repairs: $2,000 per year
- Operator Wages: $1,200 per week
- Factor in Contingencies:
- Add a 10% contingency allowance to the total estimated cost.
Example 2: Estimating Costs for a Crane
Suppose you need a crane for a construction project. Here’s how you would estimate the costs:
- Determine Equipment Needs: Identify the specific type and model of crane required for the project.
- Research Equipment Prices: Obtain quotes from multiple suppliers for purchasing or renting the crane.
- Calculate Ownership Costs:
- Purchase Price: $500,000
- Financing Costs: $10,000 per year
- Insurance: $6,000 per year
- Taxes: $4,000 per year
- Depreciation: $40,000 per year
- Estimate Operating Costs:
- Fuel: $800 per week
- Maintenance: $2,000 per month
- Repairs: $4,000 per year
- Operator Wages: $2,000 per week
- Factor in Contingencies:
- Add a 10% contingency allowance to the total estimated cost.
Conclusion
Accurate equipment cost estimation is a critical aspect of successful construction project management. By understanding ownership and operating costs, following a systematic estimation process, and avoiding common pitfalls, you can ensure that your project stays within budget and on schedule. Utilizing historical data, leveraging technology, and collaborating with experts can further enhance the accuracy of your estimates.
For those seeking more guidance and resources, consider signing up for our newsletter or exploring our advanced cost estimation tools designed specifically for construction professionals. Good luck with your next project!
FAQs
What is equipment cost estimation?
Equipment cost estimation involves calculating the expected costs of acquiring and operating equipment for a construction project. This includes ownership costs (purchase price, financing, insurance, taxes, depreciation) and operating costs (fuel, maintenance, repairs, operator wages).
How do you calculate ownership costs?
Ownership costs are calculated by summing the purchase price, financing costs, insurance, taxes, and depreciation of the equipment. These costs are typically fixed and do not vary with the amount of equipment usage.
What are operating costs?
Operating costs are variable expenses that depend on the equipment usage. They include fuel costs, maintenance, repairs, and operator wages. These costs can fluctuate based on how frequently the equipment is used.
Why are contingencies important?
Contingencies are important because they account for unexpected expenses or price fluctuations that may arise during a project. Including a contingency allowance in your cost estimate helps ensure that you stay within budget even when unforeseen costs occur.
How can technology help in equipment cost estimation?
Technology can streamline the equipment cost estimation process by providing specialized software and tools for accurate calculations. These tools can generate detailed cost breakdowns, automate calculations, and provide data-driven insights that enhance decision-making.